INTEGRATED LOGISTICS SUPPORT (ILS)
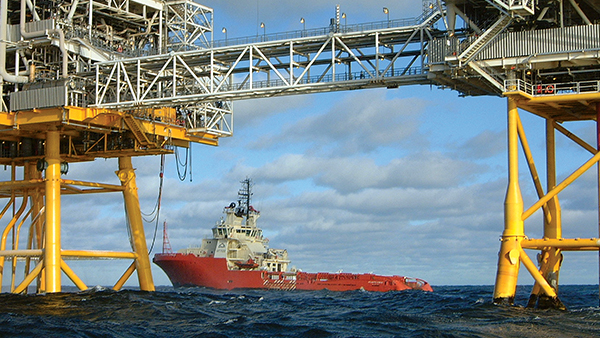
Integrated Logistics Support (ILS)
The primary goal of ILS, also referred to Integrated Product Support (IPS) is the design and implementation of an effective product support solution; reducing product life cycle cost through design influence, maintenance planning, availability and reliability enhancement, training, technical documentation, and optimization of spares availability and location.
Fleetway, as one of the largest ILS companies in Canada, draws on 40 years of history and solutions in such projects as the design and build of the Canadian Patrol Frigates, Halifax Class In-Service Support, Arctic Offshore Patrol Ship design and build effort, as well as developing the supportability elements of the future of the Royal Canadian Navy surface fleet, represented by the Canadian Surface Combatant
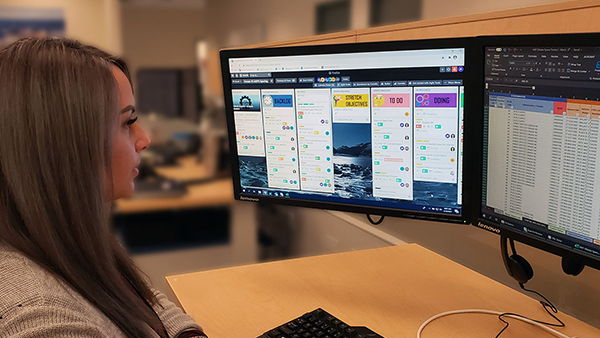
Support Planning
Develop and manage complex support system documentation including logistics support concepts, integrated logistics support plans, asset management plans, logistics support analysis plans, and publication management plans.
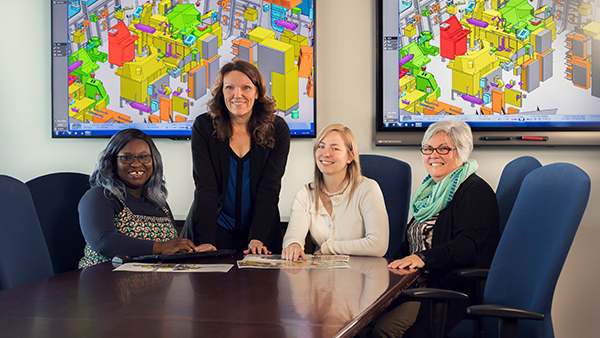
Technical Documentation Development
Through the development of interactive electronic technical manuals (IETM) or interactive electronic technical publications (IETP), following the S1000D standard, excellence in ILS early in program design and implementation effectively guides thousands of suppliers to provide the necessary operating, maintenance and digital metadata, so essential to modern in-service support efforts.
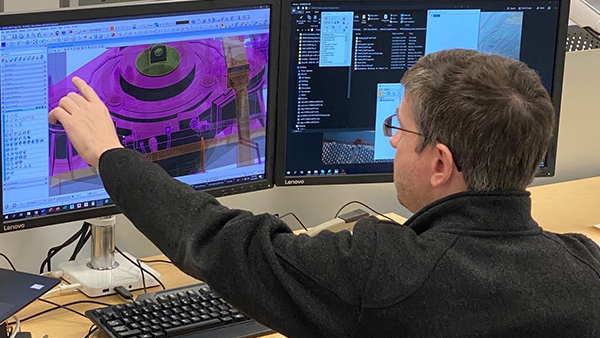
Life Cycle Cost (LCC) Management
In an environment of declining budgets, obtaining the appropriate balance between procurement of new systems and sustaining current and legacy systems is extremely challenging and requires careful analysis to effect cost reductions.Fleetway LCC studies form an integral part of the cost control and reduction effort. Analysis of the through life costs associated with the management of operations and maintenance, implementation of engineering decisions and changes to the supply chains to identify cost drivers, inform key decision makers and develop strategies to minimize through life support costs.
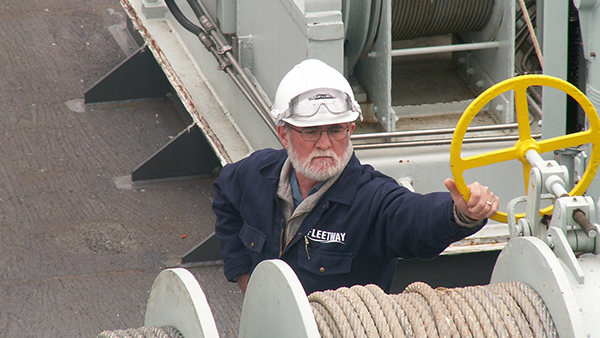
Logistics Support Analysis
Application of tailored analysis to develop or improve support system efficiency and effectiveness, including preventive, predictive and corrective maintenance planning analysis includes failure modes, effects and criticality analysis (FMECA), reliability centered maintenance analysis (RCMA), level of repair analysis (LORA), use studies and supportability analysis. The output is the foundation for Logistic Support Analysis Records (LSAR).
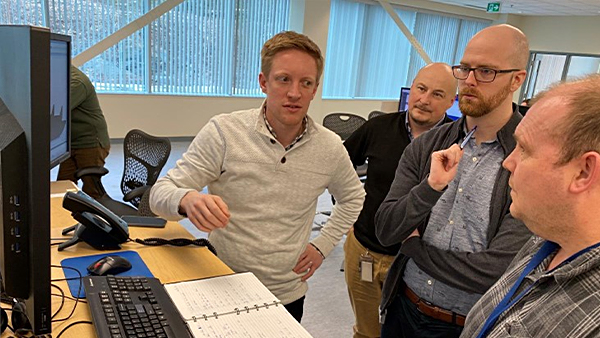
Reliability Engineering
Conduct of reliability, availability and maintainability analysis to reveal the root causes of system failure to underpin development of capability performance improvement.
Root cause analysis (RCA) is a tool designed to help identify not only what and how an event occurred, but also why it happened. Only when determination of why an event or failure has occurred will workable corrective measures be specified that prevent future events. Understanding why an event occurred is the key to developing effective recommendations. Fleetway ILS employs several techniques to perform RCA, including 5 why’s, Pareto analysis, fault tree analysis, and others
Using advanced software tool and utilizing historical data, Fleetway ILS can develop reliability block diagrams (RBD) of the system or platform. Building on historical maintenance data, reliability figures and manpower usage, a current state of availability can be baselined. Taking the results of reliability, availability, maintainability (RAM) analyses, maintenance task rationalization (MTR) exploration and resultant reduced spares and subsequent life cycle cost reduction, a projection of future availability can be predicted, and equally important, costed.
The benefits of RAM analyses, spares forecast, parts usage, manpower time and cost (along with other factors) can assist in determining those items deemed “worst offenders” contributing to the decreased availability of the system and the fleet. By focusing on those worst offenders, Fleetway ILS can provide recommendations to improve those criteria, and thereby increase fleet availability with cost effectiveness and efficiency.
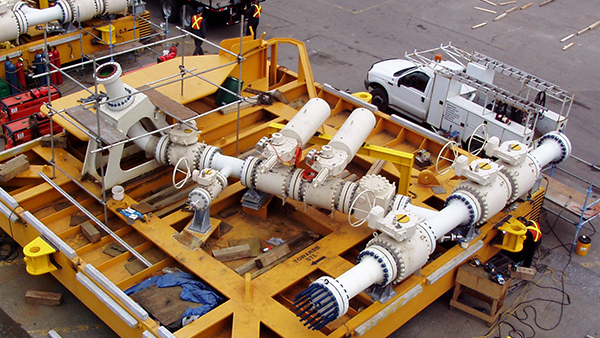
Inventory Optimization and Disposal
Critical analysis and audit of inventory holding and underpinning supply chains to develop recommendations for optimized strategic and tactical level spares holdings to meet capability outcomes.
Initial provisioning (IP) comprises assessing data for the range of spares required to meet the availability requirements; the quantity needed to support the main equipment in the early period of service, and special tools and test equipment (STTE) required to support 1st and 2nd level maintenance
As maintenance, parts vendors and other factors have changed over the past decades, the IP may no longer be valid. Fleetway ILS group conducts sparing analyses to identify anomalies and provide recommendations to rectify the issue. By reviewing the historical data of items sent to repair & overhaul (R&O) facilities, a sparing forecast of future items inducted to R&O can be determined. Pre-planning of inducted items can result in prioritized costs or even deferred costs, providing significant financial savings as costs are more wisely dispersed.
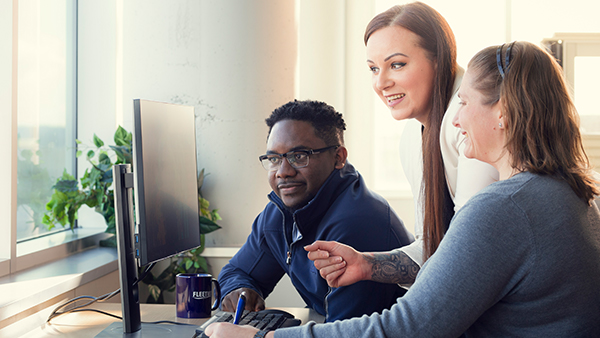
Obsolescence Management
The general concept for obsolescence management at Fleetway is to structure processes and establish an engineering system of forecasting equipment supportability and obsolescence issues at the appropriate level.Fleetway ILS continuously identifies part obsolescence issues before they affect availability of the fleet.
Through proactive obsolescence management, day-to-day vigilance, life cycle data tracking and logistics monitoring capabilities, the obsolescence problems are identified early, permitting stakeholders to mitigate and implement solutions. This proactive action enables Fleetway ILS to prevent any unexpected materiel concerns during the equipment operation.
Develop obsolescence and diminishing manufacturing sources and material shortages (DMSMS) management strategies that are integrated into technical solution design, development, production and in-service support. Obsolescence management is provided through monitoring availability of spares and components. Notifications are provided to customers through regular obsolescence management reports and meetings, ensuring system through-life support is maintained.